Method of Choosing the Best Drill Bits for Your Drilling Work
In mechanical processing, drilling work processing accounts for about 1/5 of the total processing amount, and drilling work accounts for about 30% of the entire hole processing. When purchasing drill bits, there will be drill bits of different colors, materials, crafts, and crafts.
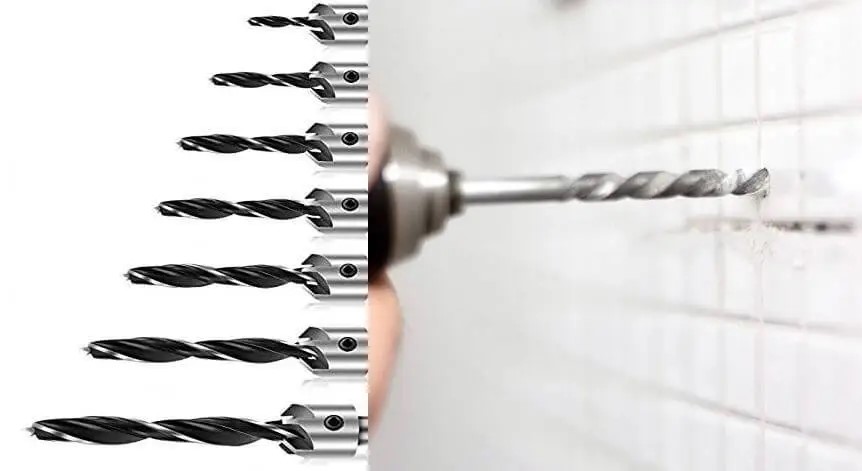
For example, here are some questions you may need to ask before purchasing drill bits:
What is the difference between the drills of different crafts?
What is the difference between the different colors of drill bits?
Is there any relationship between the color and the quality of the drill bit?
Which color drill bit is better?
1, Choosing the drill bits according to the appearance of drill bits Color and appearance.
For example, Is there any relationship between the drill bit's color and its quality? The different colors are mainly due to different processing techniques.
Drill bits in White color:
High-quality, fully ground high-speed steel drill bits often appear in white. Rolled drill bits can also achieve white by fine grinding the outer circle.
It is high quality because the quality control during the grinding process is also quite strict, and the material itself. No burns will appear on the surface of the tool.
Drill bits in Black color:
The black drill is a drill bit that has been nitrided. It is a chemical method that puts the finished tool in a mixture of ammonia and water vapor and heats it at 540~560°C to improve its durability. (There are also black drill bits on the market, most of which are just black (to cover the burn or black skin on the surface of the tool), but the actual use effect has not been effectively improved).
You can find black color drill bits from HEYGO; our drill bits are indeed nitrided. (Can record a video)
Drill bits in Gold color:
The gold color drill bit is plated with titanium nitride, divided into decorative plating and industrial plating. The decorative plating does not affect at all, but the color is golden.
Drill bits in Tan color:
Generally, cobalt-containing diamonds will make this color. Originally white, it is produced by grinding, and when it is atomized in the later period, it is made into yellowish-brown (generally called amber) M35 (Co 5%).
2, Choosing the drill bits according to the material of drill bits
The market's common materials used for drill bits are 4241/4341/9341/6542/M35/M42, and their performance increases sequentially.
4241/4341 Material
This drill bit material is suitable for drilling ordinary metals, such as iron, copper, aluminum alloy, and other low- and medium-hardness metals, and wood, but not ideal for drilling high-hardness metals such as stainless steel and carbon steel.
The quality is reasonably good within the scope of application, suitable for wholesale sales in hardware stores.
9341 Material:
This material is suitable for drilling ordinary metals, such as iron, copper, aluminum alloy, and other metals and wood. It is ideal for drilling thin stainless steel plates. Thick ones are not recommended. Within the scope of application, the quality is medium.
6542 Material:
This material is suitable for drilling various metals, such as stainless steel, iron, copper, aluminum alloy, and other low- and medium-hard metals and wood. The quality is medium to high within the scope of application, and the durability is very high.
M35 cobalt-containing material:
This material is currently the best grade of high-speed steel on the market. The cobalt-containing guarantees the hardness and toughness of the high-speed steel. Suitable for drilling various metals, such as stainless steel, iron, copper, aluminum alloy, cast iron, 45# steel, other metals, and different soft materials such as wood and plastic.
The quality is high-end, and the durability is more excellent than any of the previous materials. If you decide to use the 6542 material, it is recommended that you choose M35. The price is slightly higher than 6542, but the absolute value.
M42:
It is usually called a high-cobalt drill because its cobalt content reaches 8%. Generally, the cobalt content added to the high-speed steel raw material is up to 8%, and more will become a cemented carbide. The purpose of adding cobalt is to improve the high-temperature resistance and abrasive resistance of the drill.
3, Choosing the drill bits according to the producing processes of drill bits
There are three processes for producing drill bits: rolling, milling, and grinding.
The central processing techniques of twist drill bits are spiral groove processing, heat treatment, and sharpening. Because heat treatment and subsequent grinding processes are the same, the main difference lies in forming the twist drill's working part.
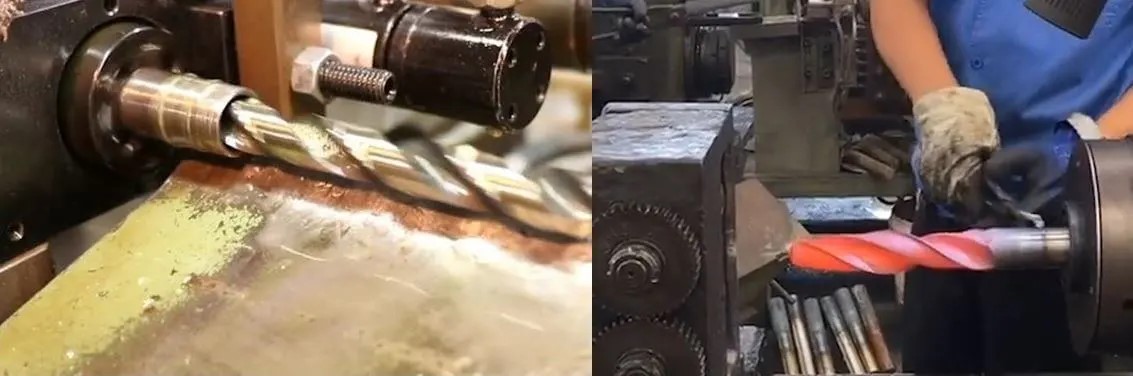
At present, it is used to make twist drill bits. There are mainly three methods in the forming process of the drilling part: milling method, rolling method, and grinding way.
Milling method for drill bits:
Use a forming milling cutter to mill the required spiral groove shape on the unhardened twist drill blank. The milling method has an extensive processing range, mainly processing 10 to 70 mm twist drills.
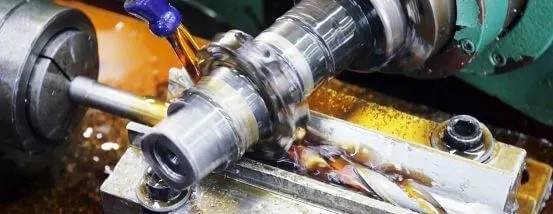
Milling method The disadvantage is that the tool's cost is high, the processing time is long, and the final shape is processed before heat treatment. The geometrical error generated during hardening is almost all reflected in the finished drill.
Rolling for drill bits:
Rolling four fan-shaped plates on the heated blank to form the shape of the drill bit. Compared with the milling method, the drill bit manufactured by plastic deformation has lower accuracy.
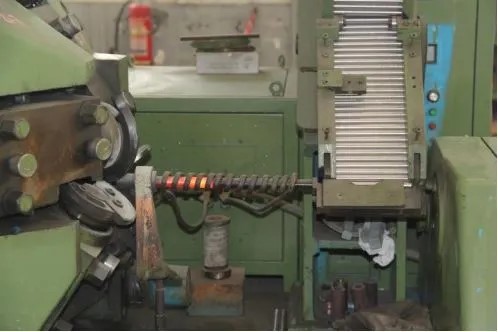
Besides, due to the geometric error caused by the heat treatment deformation to the rolled twist drill, it cannot meet the requirements of drilling high-quality holes. This method's advantage is mainly to save the raw materials for manufacturing twist drills, so the economy is good. The maximum diameter of the four-roll rolling method is 40mm.
Grinding for drill bits:
When the grinding wheel's speed reaches 100m/s, the latest one makes it a reality to grind the spiral groove of the twist drill from the whole material. High-speed grinding can reduce the cutting force and significantly improve the surface quality, and reduce Shape error.
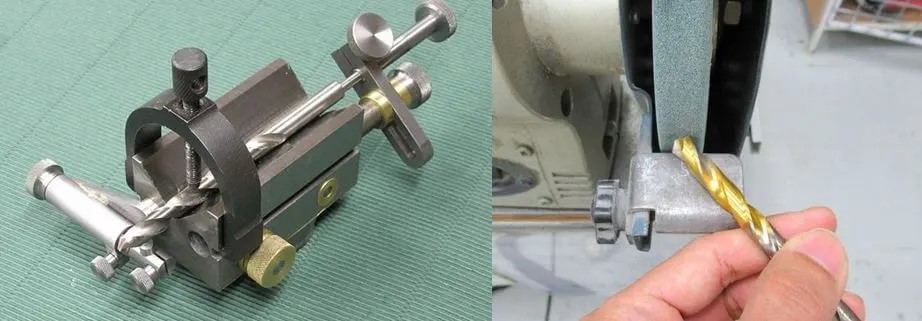
Compared with the milling method, the grinding method can significantly reduce the single-piece working hours, and the quality is high and stable. At present, the grinding method can only manufacture twist drills with a diameter of less than l5.
What're their differences and characteristics?
Technical analysis and economic effects of three processing techniques:
1. Technical indicators
|
|
Milling |
Rolling |
Grinding |
Roughness Ra(μm) |
Cutting edge |
4.6 |
6.5 |
2.5 |
Blade groove |
8.6 |
12.5 |
3.2 |
|
The symmetry of the blade |
|
0.105 |
0.301 |
0.03 |
Radial runout |
|
0.05 |
0.08 |
0.03 |
Normal jump |
|
0.05 |
0.18 |
0.03 |
2. Processing efficiency
Because the processing technology of twist drills is the same except for spiral grooves, other processing procedures are the same. For this reason, only the processing time of their spiral grooves is compared. A few examples of processing 12mm straight shank twist drills in one hour.
Processes |
Milling |
Rolling |
Grinding |
Processing efficiency |
18 |
250 |
98 |
3. The ground twist drill has high dimensional accuracy and uniform quenching hardness. The bending deformation is small, and the twist drill has been subjected to compressive stress during processing.
In the milling processing method, the twist drill is subjected to tensile stress, rolling. In the rolling and extrusion processing methods, the temperature is difficult to control, + high-speed steel materials are prone to decarburization, cracks, etc., which affect the twist drill's service life.
Later, the wear value of the blade surface is VB--0.15 mm as an example, the wear test of the l2 straight shank twist drill under the same conditions as the twist drill.
Processes Milling Rolling Grinding
Number of holes 28 25 34
Experimental conditions:
(1) Processing material: oyster steel quenched and tempered, HB-l90-200
(2) Drilling parameters; V=30m/rain, f-0.28mm/r, hole 36mm deep, no through-hole.
(3) Cutting fluid: emulsified oil aqueous solution
4. Economic effect
Milling method
The production efficiency of this processing method is relatively low. It is only suitable for single-piece small-batch production. The milling cutter has a complex structure, high price, and many procedures.
Rolling
The material utilization rate is about 25 higher than milling; the production efficiency is more than ten times higher than milling; it is suitable for mass production.
However, this type of method's production environment is less safe; when changing specifications, it is difficult to adjust the process; each process The parameter contradiction is prominent, and the rejection rate is high.
Grind
The production efficiency is higher than that of the milling method; the bending deformation is eliminated. The straightening process is saved; the processing accuracy is high, and the quality is stable. The rate of waste and defective products is shallow.
The equipment price is high. The processing range is small, and it is difficult to add chips.
Therefore, based on the above data, the high-speed steel grinding drill bit is compared with the rolling and milling process in the following points:
1, The geometric precision of the ground drill is high. Using rolling and ton-making technology, the groove processing of the drill bit must be completed before quenching. The geometric accuracy of the drill bit is reduced due to the deformation of the quenching treatment.
The grinding process grinds the grooves after quenching, eliminating the deformation caused by the quenching treatment and improving the drill bit's geometric accuracy. This allows the drill bit to be more finely divided into specifications and sizes to meet the precise processing of different sizes.
The improvement of the drill bit's smoothness only improves the aperture and smoothness of the processed parts.
2, Long service life of ground drills. The practice has proved that the ground drill bit's service life is 1~2 times longer than that of the rolling and baht drill bit. This is related to the excellent precision of the ground drill bit, high brightness, sharp cutting edge.
3, High production efficiency. Now the grinding process has developed to the stage of powerful grinding, and the production efficiency of machining drills has reached 2 to 5 times that of milling.
Generally speaking:
In terms of accuracy/finishes/cost, the three processes are all increasing. Rolling<milling<grinding
Whether it is an end-user, a distributor, or a big brand customer, we can also consider the following points when choosing the suitable drilling soil and supplier.
Whether it is a well-known brand
Quality of upstream suppliers
Building time
Heat treatment
Machining
Quality control awareness
Detection awareness
Multi-batch testing to verify its stability